Introduction
If you’re searching for the cost to build a 10,000 sq ft steel warehouse in 2025, you’re not alone. It’s a common question with a not-so-simple answer. While it might be tempting to hunt for a quick number, the truth is that warehouse construction costs hinge on a range of factors. Spoiler alert: the final price isn’t what matters most—the value is. And when it comes to value, buying factory direct from SteelBuilt Direct is where the smart money goes.
In this in-depth guide, we’ll explore what goes into the cost of a 10,000 sq ft prefab steel warehouse. We’ll also unpack the hidden variables, budgeting considerations, and real-world insights you won’t get from a simple price-per-square-foot chart. So grab a cup of coffee and settle in. This is the guide every business owner, builder, and developer needs before pulling the trigger.
1. The Misleading Simplicity of “Cost Per Square Foot”
You’ve probably come across numbers like $25, $50, or even $80 per square foot. That range could put your 10,000 sq ft warehouse somewhere between $250,000 and $800,000. But what do those numbers actually include? Spoiler: sometimes not much.
Square foot pricing rarely accounts for:
- Site preparation
- Insulation and HVAC
- Interior buildout
- Doors, windows, and finishes
- Freight and delivery
- Erection and labor
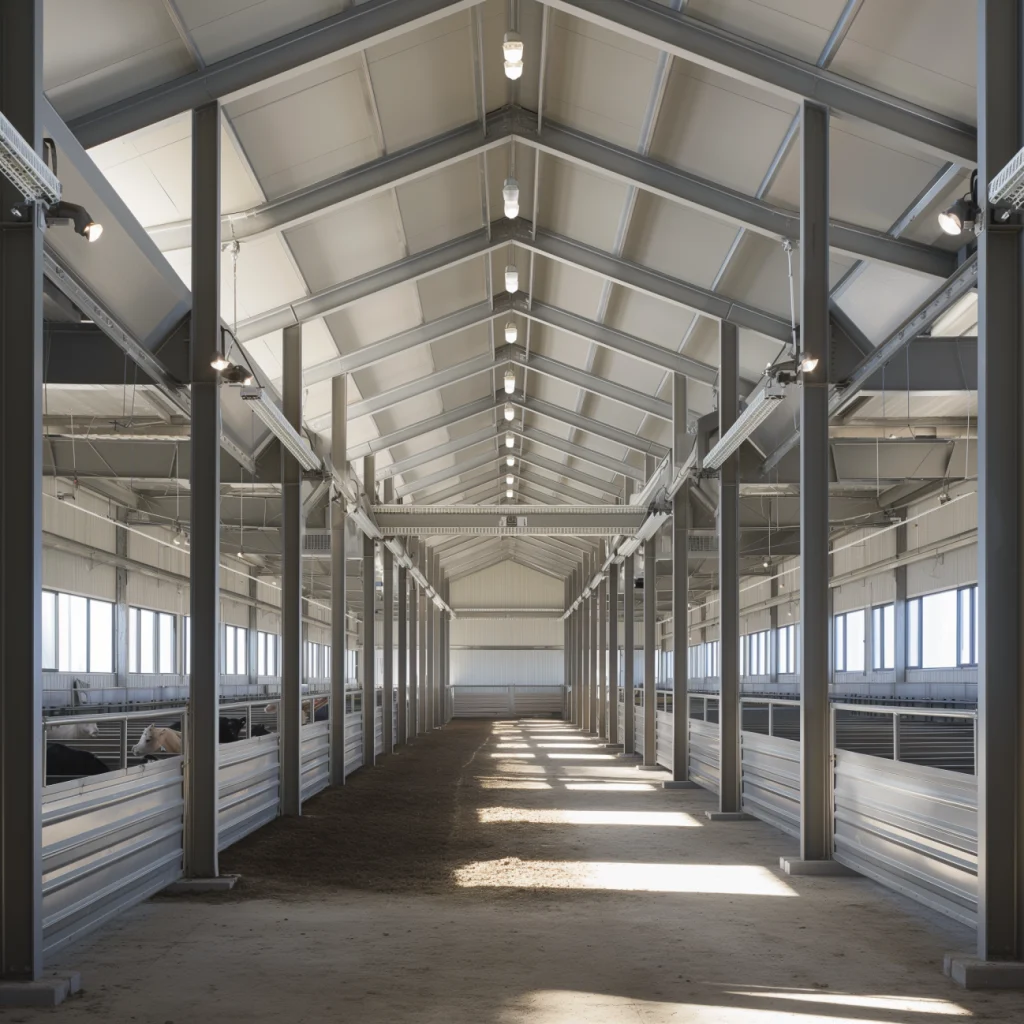
So while a base building kit might technically start at $25/sq ft, real-world projects can add up fast. That’s why it’s more useful to understand the moving parts rather than cling to a magic number.
2. Key Cost Drivers for a 10,000 Sq Ft Steel Warehouse
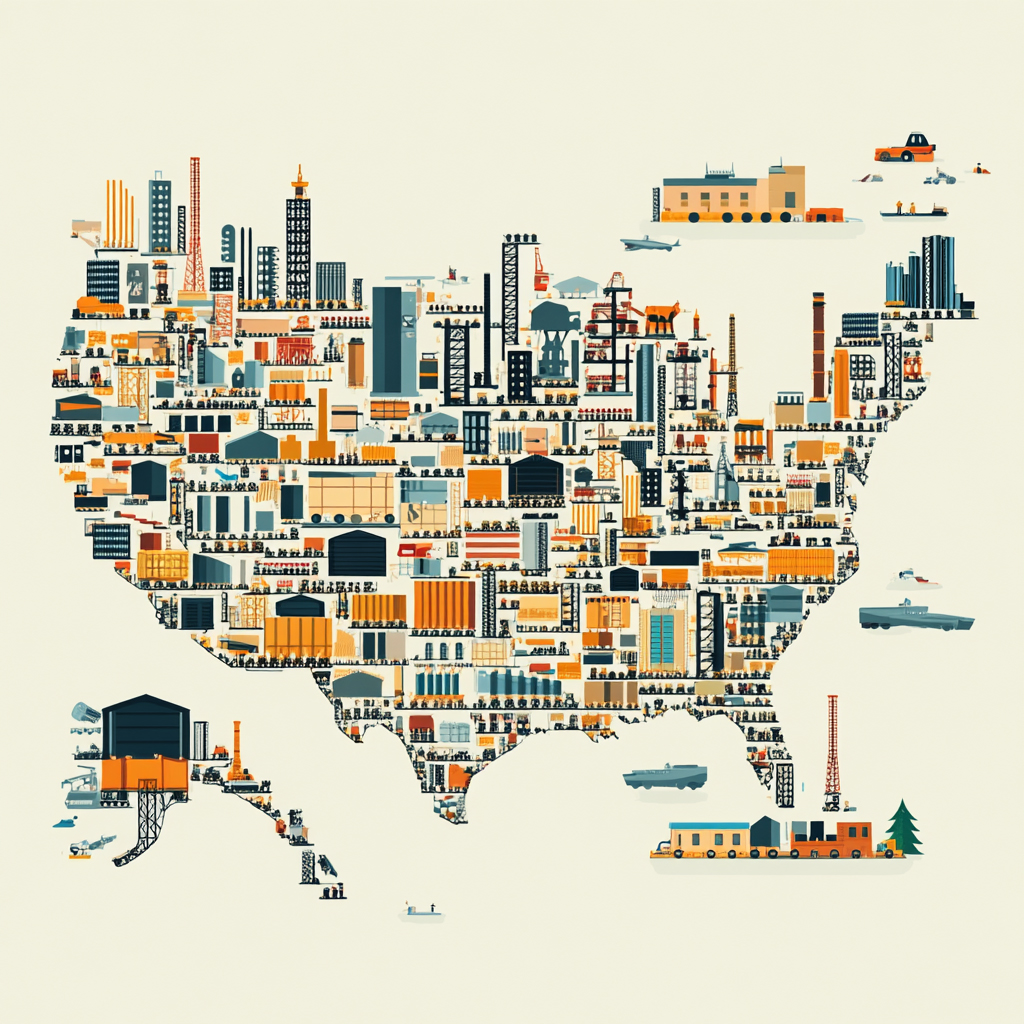
A. Location, Location, Location
Where you build influences labor costs, permit fees, code requirements, and delivery logistics. A rural build in the Midwest will look very different on paper than a project in a coastal city.
B. Design Complexity
Will this be a simple storage building or a facility with office space, mezzanines, multiple bays, and dock doors? Design sophistication affects everything from framing and anchoring to material selection.
C. Intended Use
Your use-case matters. A cold storage warehouse will have very different needs (and costs) than a light manufacturing plant or e-commerce distribution center. Think electrical load, insulation R-values, ventilation, and safety requirements.
D. Site Preparation & Foundation Work
Clearing land, grading, soil tests, and pouring a proper foundation are substantial costs often overlooked in early budgeting.
E. Building Codes and Engineering
Different states and municipalities enforce different seismic, wind, and snow load codes. Your steel building must be engineered to comply, which can affect steel gauge, framing systems, and cost.
3. Why Prefab Steel Makes Financial Sense
Prefab steel buildings aren’t just faster to erect; they’re smarter investments. You benefit from:
- Shorter construction timelines
- Reduced labor expenses
- Lower lifetime maintenance
- Energy efficiency (when insulated properly)
- Modular expandability
And the more square footage you build, the more you save per square foot thanks to economies of scale.
4. Real-World Pricing Examples (Hypothetical Scenarios)
Let’s look at three scenarios to give you an idea of how widely prices can vary:
Scenario A: Basic 10,000 Sq Ft Warehouse in Kansas
- Use: Agricultural storage
- Simple design, no insulation, single-slope roof
- Estimated total cost: ~$350,000
Scenario B: Mid-Tier Distribution Center in Texas
- Use: Regional logistics hub
- Dock doors, office space, insulation, HVAC
- Estimated total cost: ~$625,000
Scenario C: High-Spec Manufacturing Facility in California
- Use: Clean-tech production
- Heavy electrical, seismic upgrades, complex interior
- Estimated total cost: ~$900,000+
Again, your mileage may vary. That’s why getting a direct quote is critical.
5. Hidden Costs to Watch Out For
Even savvy buyers overlook these:
- Local permit fees and impact studies
- Utility connections
- Equipment installation (cranes, conveyors, etc.)
- Travel and lodging for erecting crews
- Change orders from poor initial planning
6. Why Buying Factory Direct From SteelBuilt Direct Matters
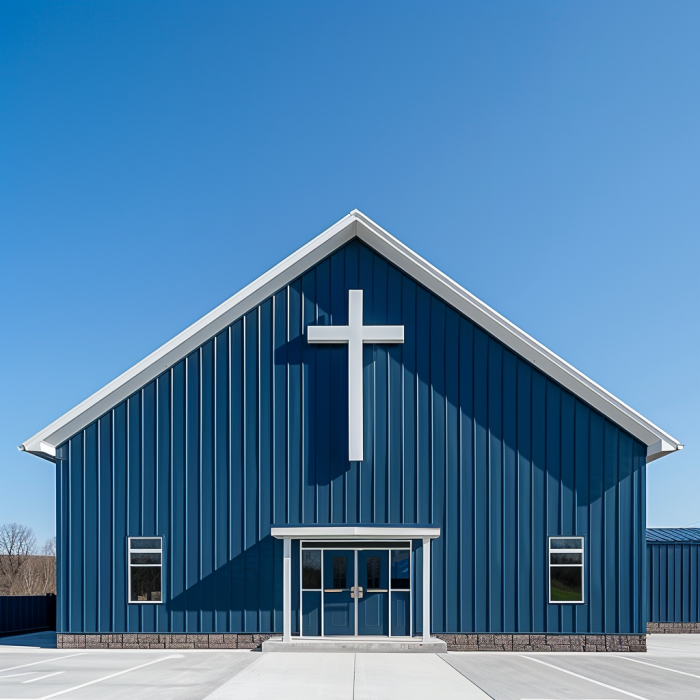
Here’s where the price conversation comes full circle. Anyone can throw out a price tag. But only a direct manufacturer like SteelBuilt Direct can deliver unmatched value:
- No middleman markups
- Engineered-to-order with expert guidance
- Faster lead times direct from our facility
- True customization for your business needs
- Transparent pricing and honest consultation
When you cut out the broker or local dealer, you get clearer communication, better pricing, and total accountability.
7. The Cost of Waiting
Steel prices fluctuate. Labor rates climb. Interest rates change. The best time to build might be now. Waiting 6 months or a year could mean paying 10% more across the board.
At SteelBuilt Direct, we help you lock in today’s pricing with options for phased builds or flexible financing strategies. Waiting might cost you more than acting today.
8. So What Does a 10,000 Sq Ft Steel Warehouse Actually Cost?
Here’s the honest truth: We can’t tell you without learning more. But we can promise that when you work with SteelBuilt Direct, you’ll get:
- The best value per dollar
- An honest assessment of all costs
- A partner who cares about your success
Our team walks with you from design to delivery—and we know how to stretch your budget without cutting corners.
Ready to Get Your Personalized Quote?
If you’re serious about building a 10,000 sq ft steel warehouse in 2025, don’t settle for guesswork. Contact SteelBuilt Direct for a free consultation and customized quote.
Let’s turn your vision into steel.
CONTACT US TODAY!
PHONE: 413-343-7999
EMAIL: info@steelbuiltdirect.com
ONLINE: STEELBUILTDIRECT.COM
SteelBuiltDirect.com — Your Direct Source for Prefab Steel Warehouses.
Write a Comment